

The Shikishi Board
Understanding Shikishi — A Series (2)
In this section, we take a closer look at the physical characteristics of a shikishi: its materials, structure, format, and traditional uses. From layered washi paper to gold-trimmed edges, this page answers the question: what exactly is a shikishi?
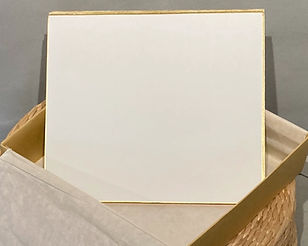
The Shikishi Board : Structure, Craftsmanship, and Material Function
The shikishi (色紙) is a traditional Japanese art board designed as both a material support and an aesthetic object in its own right. While often associated with the elegant presentation of poetry, calligraphy, and ink painting, the shikishi is also a highly refined craft item, embodying centuries of artisanal knowledge in papermaking, mounting, and decorative finishing.
At its core, a shikishi board is a laminated object. It begins with a thick backing made from multiple layers of hand-pasted paper (often recycled washi) or, in modern versions, lightweight composite board. Over this base, a facing layer of high-quality washi paper is applied with a natural adhesive. The finished surface is carefully dried under pressure to eliminate warping, and then burnished to achieve an even, receptive finish suitable for ink, pigment, or pencil.
The edges of the board are traditionally wrapped in a narrow strip of gold foil (or occasionally silver or patterned metallic paper), a decorative feature known as kinbari (金貼り). This gilded border not only enhances the aesthetic presence of the board but also visually delimits the pictorial or calligraphic space. The reverse side is often covered with colored or patterned paper to complete the object’s decorative unity.
Unlike scrolls, which are designed to be rolled and stored, shikishi are rigid and flat, meant to be handled, mounted, framed, or presented as standalone artworks. Their construction balances durability with elegance, enabling the board to function both as a practical support for fine brushwork and as an autonomous visual object.
The sizes of shikishi vary more than is commonly assumed. While the most iconic dimensions (approximately 24 x 27 cm) became standardized during the Edo period for calligraphic dedications and formal presentation, a wide array of formats coexist within the broader category of shikishi-type boards—including smaller mini-shikishi (typically around 12 x 13.5 cm), narrow tanzaku used for poetry, and larger formats for ceremonial or collaborative use.
Contemporary artisans and manufacturers, both in traditional craft centers like Mino and through industrial production, continue to supply a wide range of shikishi, with surfaces adapted to various media including watercolor, acrylic, oil pastel, and mixed media.
As a medium, the shikishi board is thus not merely a neutral substrate but a historically and materially rich surface—imbued with the tactile legacy of Japanese papermaking, mounting arts (hyōgu), and decorative tradition. In modern artistic practice, it offers a hybrid space: intimate yet formal, conventional yet open to reinvention. Its format invites artists to engage not only with image-making but with the medium’s own historical codes and material specificity.
Traditional Fabrication Process
The making of a shikishi board typically involves several meticulous steps:
-
Core preparation: A multi-layered paperboard or composite base is prepared for rigidity and lightness. In traditional settings, recycled washi may be layered and pressed by hand.
-
Surface mounting: A high-quality sheet of washiis adhered to the board using a natural starch-based glue.
-
Drying and pressing: The board is pressed flat and allowed to dry under controlled conditions to prevent warping or bubbling.
-
Burnishing: Once dry, the surface is lightly burnished to produce a smooth, receptive texture suited to ink or pigment.
-
Edge finishing: A strip of gold foil (kinbari) is applied to the edges, enhancing the board’s visual framing.
-
Backing: The reverse side is finished with decorative or neutral paper to complete the board aesthetically.
Each of these steps reflects a tradition of craftsmanship passed down through generations of paper-makers and mounters, particularly in historic production regions like Mino, Echizen, and Kyoto.
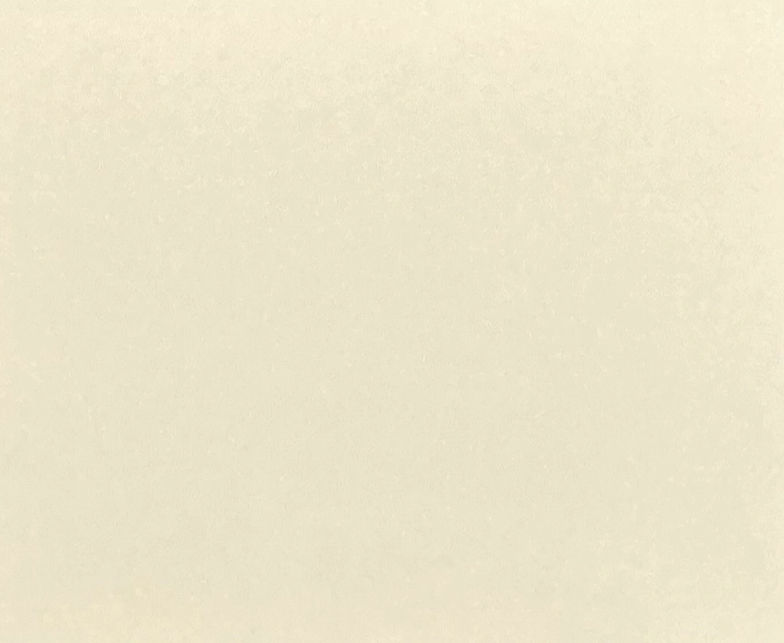